Illuminating the Best Countersink Bit Features for Metal Usage
Achieving a professional finish when working with metal often requires drilling countersunk holes for screws and fasteners. Using the right countersink bit for your application is key to efficiency and quality results.
As we explore the optimal countersink bits for metal usage, we will shed light on key features and considerations in choosing the best bit for your needs.
Introduction to Countersink Bits and Their Uses with Metal
What is a Countersink Bit and Why Use One for Metalworking?
A countersink bit is a specialized drill bit used to create angled holes that allow screw and bolt heads to sit flush within the surrounding material. The bit cuts a conical recess around the hole, leaving a clean finish with minimal surface irregularities.
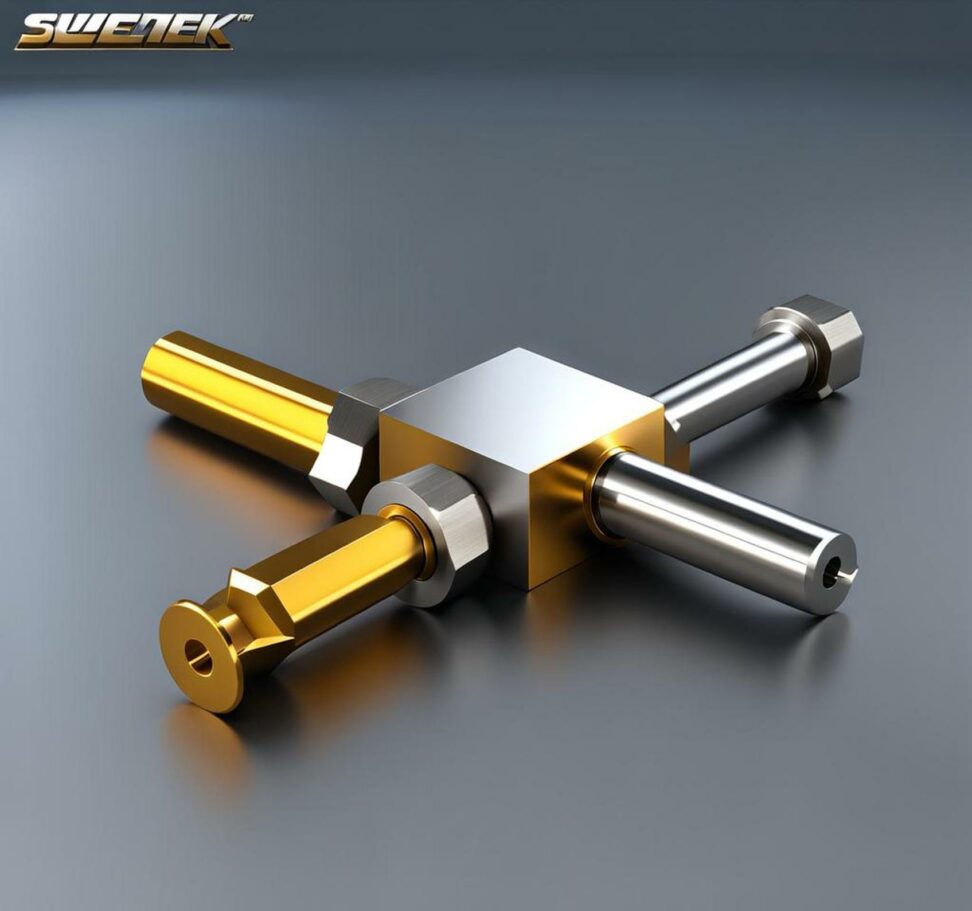
For metalworking applications, countersinking provides numerous benefits:
- Allows flush mounting of fastener heads for a smooth appearance
- Removes rough top edges to prevent injury from sharp metal burrs
- Increases stability and strength by enabling full contact between joining materials
Common Materials Used to Make Countersink Bits for Metal
Countersink bits designed for metal applications are commonly made from hardened tool steel alloys. The most popular options include:
- High carbon steel - Durable and long-lasting
- High speed steel (HSS) - Enhanced heat/wear resistance
- Solid carbide or carbide tips - Extreme hardness for smooth cutting
Factors to Consider When Selecting a Bit for Your Project
Choosing the optimal countersink bit depends on several factors:
- Type of metal being drilled
- Diameter of the screws/bolts being used
- Desired finishing result (surface smoothness)
- Frequency of use (durability needs)
Considering these metrics will guide you towards the ideal bit for your particular metalworking application.
Countersink Bit Materials - Pros and Cons
High Carbon Steel Bits
High carbon steel offers durability and longevity at an affordable cost. The high carbon content enables the bits to maintain decent sharpness for reasonable cutting smoothness.
While certainly sufficient for light duty DIY use, high carbon steel lacks the hardness for heavy repetitive metal machining over time before requiring sharpening. It is best suited for occasional workshops or home uses.
High Speed Steel (HSS) Bits
The addition of elements like tungsten, vanadium and molybdenum give HSS bits enhanced strength and resistance to generated heat. This allows faster drilling speeds without losing cutting ability or softening from high temperatures.
The improved heat tolerance also minimizes the need for frequent resharpening. HSS is significantly more durable than basic carbon steel, making it a popular choice for metalworking shops and industrial applications.
Solid Carbide and Carbide-tipped Bits
For extremely hard metals like stainless steel, solid carbide or carbide-tipped bits are often viewed as the premium option. Pure carbide maintains sharpness exceptionally well across extended high-speed operation.
However, solid carbide lacks impact resistance and is brittle. This makes it ill-suited for handheld use in riskier applications. Carbide-tipping offers improved durability through added toughness from softer metal behind the incredibly hard cutting surface.
How Materials Impact Performance with Metal
When countersinking metal, a few key advantages emerge across bit materials:
Material | Hardness | Sharpness Retention | Durability |
High Carbon Steel | Low | Low | Medium |
HSS | Medium | Medium | High |
Solid Carbide/Carbide-Tipped | Very High | Very High | Low (Carbide) / Medium (Tipped) |
Harder materials retain edges better for smooth cuts, while more durable steels handle repetitive tasks. Consider costs, tasks, and metals involved when deciding on the optimal balance of features.
Key Design Elements that Impact Countersink Bit Performance
Flute Count and Helix Angle
Multiple flutes, or cutting edges, provide enhanced chip clearance while drilling. This prevents binding and overheating. More flutes yield smoother, faster hole boring.
Helix angles in the flute geometry also impact cutting sharpness and swarf removal. Bits with higher helix angles clear chips efficiently for clean cuts.
Countersink Angle
Matching your countersink's angled taper to the screws used is vital for proper flush fitting. Most common countersink angles are:
- 82deg - For standard flathead screws
- 90deg - Optimized for metric socket and cap screws
- 100deg-110deg - Ideal for specialty flathead screw types
Diameter Considerations
Choosing a countersink bit with a diameter approximating the width of your screws' heads allows accurate piloting and a snug fit. A tight tolerance here prevents loose or uneven setting.
Overall Construction and Durability
Seeking countersinks made from quality machined steel, with securely attached carbide cutters if tipped, ensures longevity under grinding metal use.
Reinforced shanks and centralized screw holes further bolster robustness. Anti-slip coatings provide grip, control, and reduce hand fatigue.
Proper Use of Countersink Bits for Best Results
Securing the Bit in the Drill Chuck
Carefully insert the countersink's shank deep into drill chuck, then tighten manually or with a chuck key. Overtightening can damage the bit once heated. Secure it tightly, but not excessively.
Setting Drill Depth for Flush Screws
Use depth stops on drill presses or workpiece guides for hand drills to set the precise countersink depth. This ensures screw heads sit evenly within surrounding material.
Workpiece Setup and Clamping
Utilize clamps, vises, or jigs to completely stabilize metals being drilled. Any vibration or shifting during operation risks wandering holes. Secure setups maintain accuracy.
Safety First - Equipment for Metal Drilling
When machining, always wear safety glasses to deflect flying swarf and burrs. Further equip yourself as able with leather gloves, ear protection, sturdy shoes, and metatarsal guards.
Operating cautiously prevents painful chips or abrasions. Prioritize personal protection throughout metalworking tasks.
Review of Recommended Countersink Bits for Metal
Top Countersink Bit Brands for Metalworking
HSS and carbide-tipped bits from reputable manufacturers offer quality results for most metalworking needs. We recommend exploring:
- Irwin
- DEWALT
- MILWAUKEE
- Bosch
These brands engineer durable bits honed to bore clean, even holes across various metal types.
Notable Bits Across Popular Price Points
Bit | Material | Price |
Irwin Countersink Bit Set (8 pc) | HSS | $$ |
DEWALT Countersink Set (3 pc) | Carbide-Tipped | $$$ |
CRAFTSMAN Countersinks (1 pc) | HSS | $ |
This sampling displays quality bits for essential countersinking needs at various investment levels.
Finding the Right Bit for Your Specific Application
Consider your budget, metal hardness, desired finish, and workload volume when selecting the optimal countersink.
High-frequency users or machinists dealing with hardened metals may benefit from pricier solid carbide or tipped bits offering extreme durability. Less active DIYers can rely on very capable and affordable HSS options.
Match bit features like flute count, angles, diameters, and materials to your countersinking purposes for the best experience.
Achieving Quality Countersunk Holes in Metal - Final Tips
Troubleshooting Common Countersinking Issues
When problems arise countersinking, refer to this diagnostic:
- Rough hole edges - Bit dulling; use lubricant; reduce feed speed
- Off-center/wandering holes - Insufficient workpiece clamping; apply steady pressure
- Screws not flush - Incorrect countersink depth set; double check measurements
Maintaining Your Bits for Continued Performance
Preserve your countersink bits by avoiding bending, properly sharpening once dull, and coating with rust protection after cleaning. Well-maintained bits yield years of smooth service.
As you advance, try different bit types and diameters to handle various screw sizes or metal stock hardnesses. Experiment with cutting lubricants as well for smoother running.
You can now use countersink bits for metal with full confidence thanks to the knowledge provided here. We aimed to illuminate the key considerations, top options, and best practices to promote your success sinking flush, accurate holes. Please reach out to us with any other questions on achieving professional countersunk finishes in your vital metal projects!